| CASE STUDY: Kustom Signals EyePortal
An Innovative In-Car Video System for Kustom Signals
Learn how Systematic developed a bespoke video streaming adapter in 3.5 months
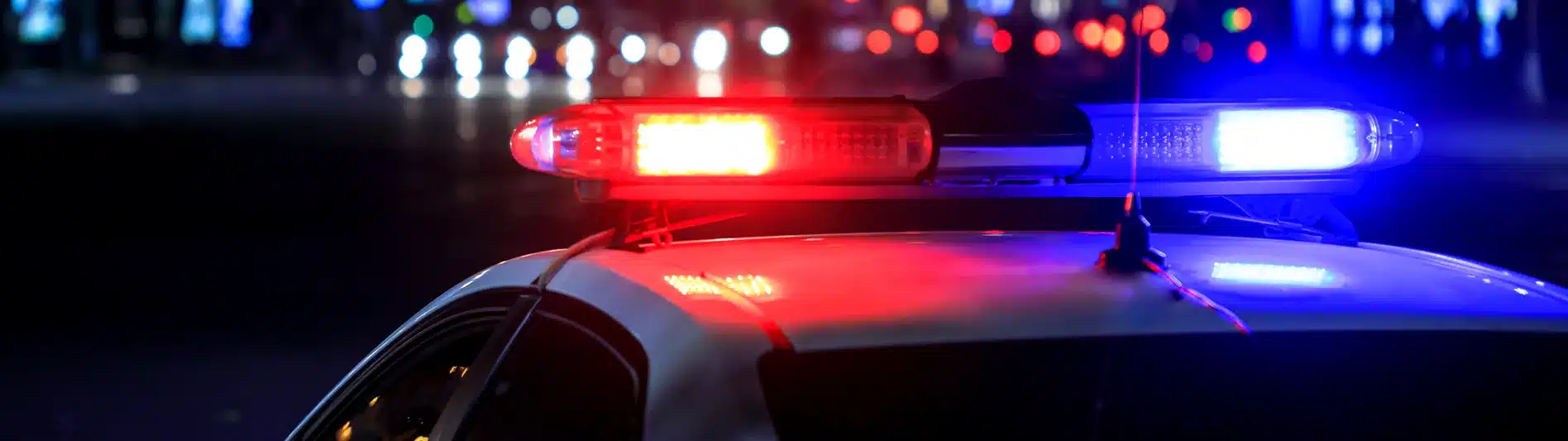
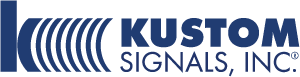
Kustom Signals has been serving law enforcement agencies with quality technology for more than 57 years.
Services
Hardware Engineering, Software Development
Project Timeline
3.5 months to Production Ready
6 months to Full Production
Tech Stack
Embedded Linux, QT Framework, C/C++, BLE, Wifi
It is very exciting to continue to innovate in ways that benefit our customers and communities. This innovation in particular is a continuation of the work we pride ourselves in.
Ryan O’Donnell
Product Manager – Video, Kustom Signals Inc. – KustomSignals.com
The Challenge
Kustom Signals has been producing rock solid electronics for law enforcement for over 50 years. When they needed help integrating their next generation wireless cameras into an in-car video system, they called Systematic Consulting Group.
The video system integration presented several challenges. The system didn’t support modern protocols and the system software couldn’t undergo major changes. Any electronics used would have to survive inside a patrol car, baking in the summer, freezing in the winter, and being subjected to severe vibration and high Gs.
Systematic proposed a hardened “portal” device, called EyePortal, which would hide all the complicated stuff and deliver video directly to the in-car system.
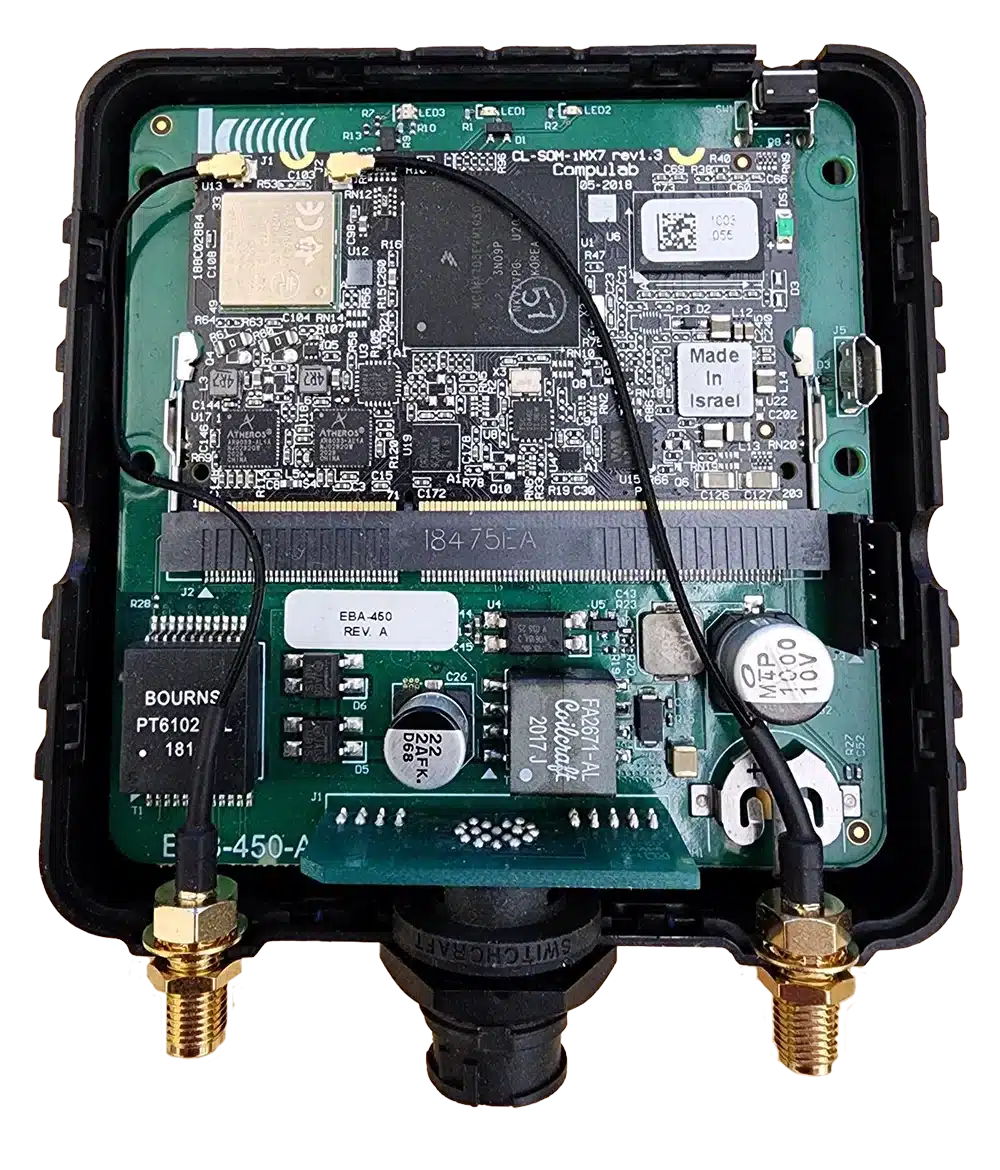
The Process
Discovery
Systematic pinned down which protocols EyePortal needed to support as well as how it would transmit that information to the system. We determined that BLE, WiFi, Ethernet, and audio decoding capabilities would all be required. We also identified a need for specialized locking connections to keep the device connected under severe accelerations. We also estimated the expected processing needs and pared the hardware down to a single core application processor, saving money.
Design
Kustom Signals specified a quick time to market and a relatively low yearly quantity, so Systematic suggested using off-the-shelf Linux SOM with a custom carrier PCB. The off-the-shelf SOM saved development time and per-unit costs, and the custom carrier board could support rugged connectors. Systematic chose a locking automotive grade connector that would allow data, power, and audio to be run over a single cable. Systematic shared these specifications with the industrial design team, who drew up a rugged but sleek case.
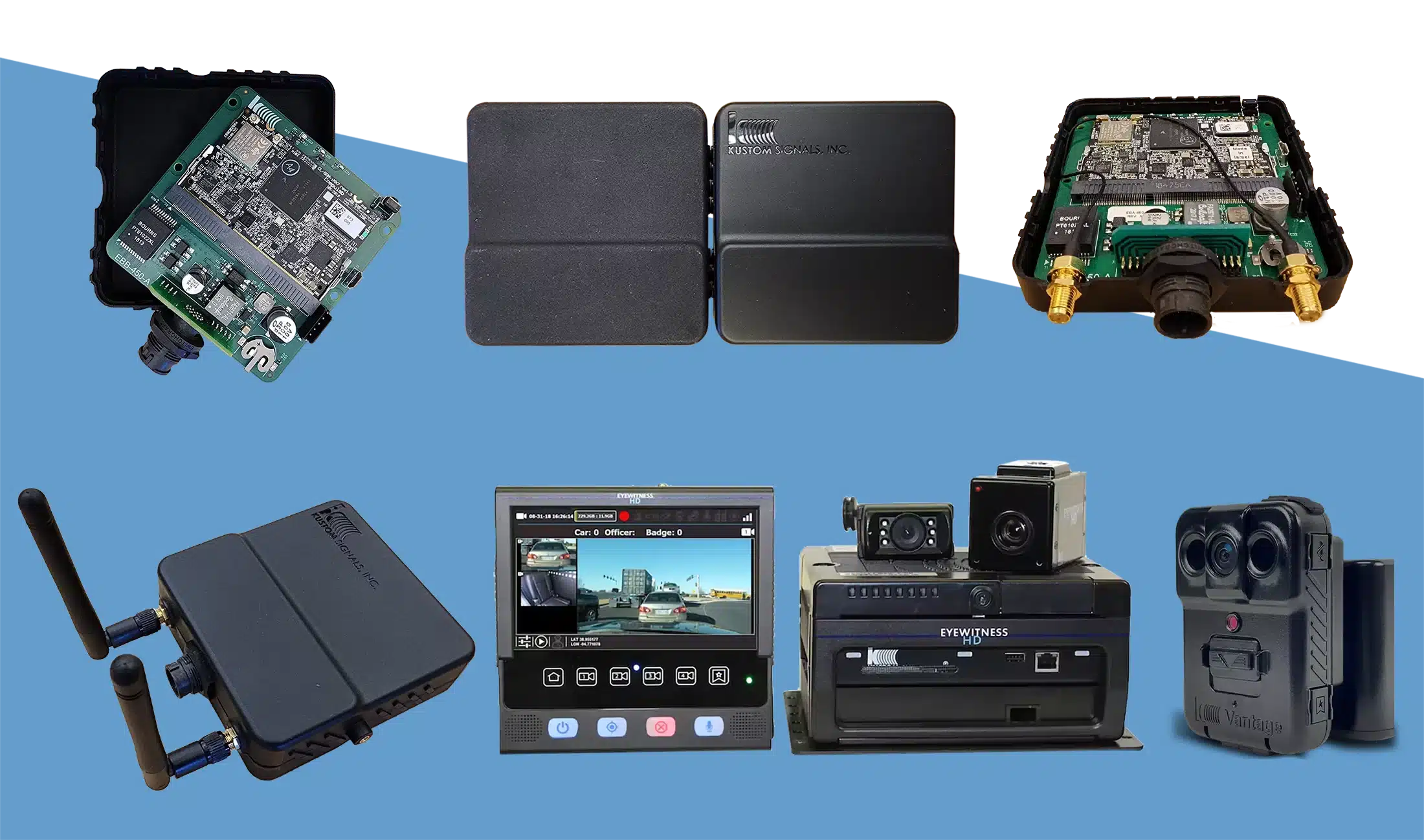
Development
With designs complete, we began schematic capture for the hardware followed by PCB layout. Once complete, the designs were reviewed for manufacturability and sent to a quick turn board manufacturer for prototypes.
Systematic immediately started software development in parallel using a SOM development board. Over 75% of the software was complete and validated prior to ever having the first prototypes PCBs in hand.
The industrial design team continued in parallel as well, and 3D printed versions of the case were ready for fit and function testing at nearly the same time the prototype hardware and software were completed.
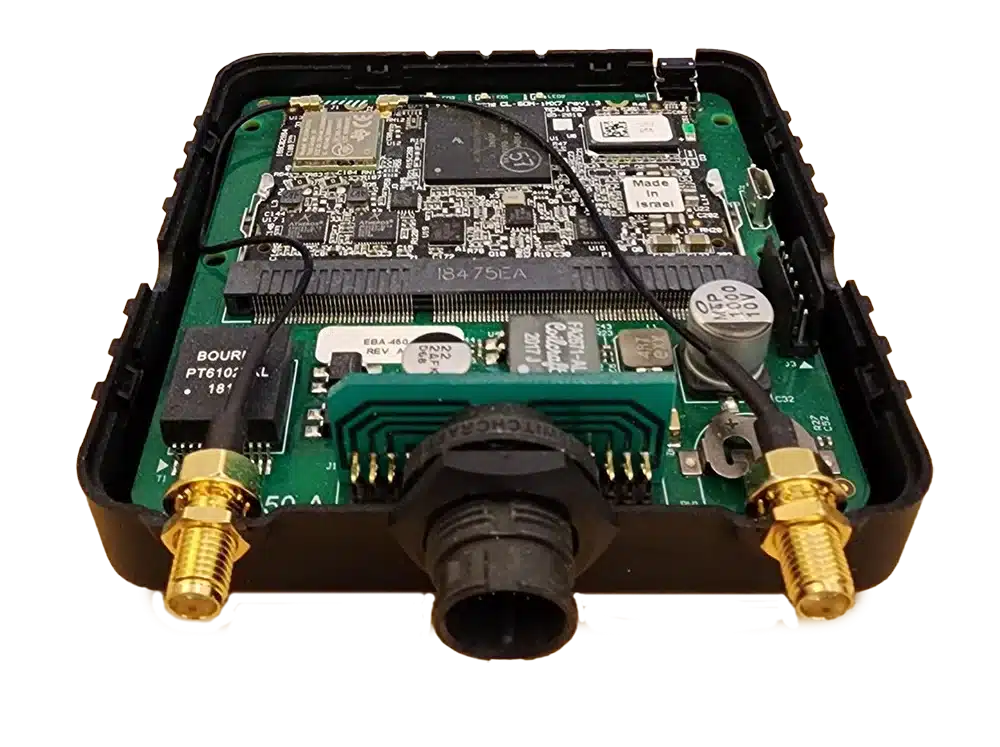
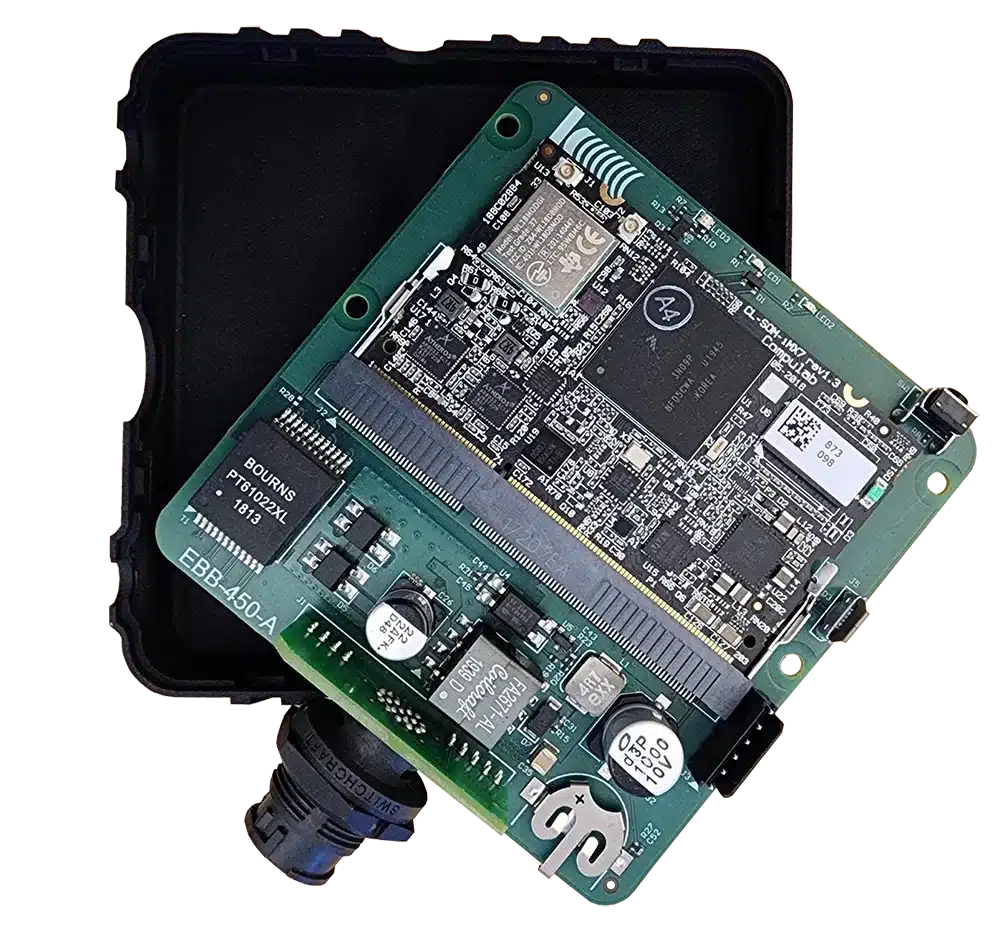
Prototype Testing
Initial prototypes consisted of a quick-turn PCB, an off-the-shelf Linux SOM, and 3D printed cases. With real components and parts in place all mechanical fittings were validated and integrated prototypes resembled the final product were built.
All hardware was validated on both benchtop and in several real scenarios while installed in a vehicle. Software was refined based on both simulated and full integration testing.
Finally, prototypes were installed in the field for validation prior to prototype sign off.
Production Ready
Once prototype testing was complete, a production image was created with the final software package and submitted to the SOM manufacturer, and cases were queued for injection molding. Systematic is particularly proud that its design files were sent off for production without modification. No issues were discovered during prototype testing.
The first EyePortal production run started 3.5 months from Systematic’s project kickoff.
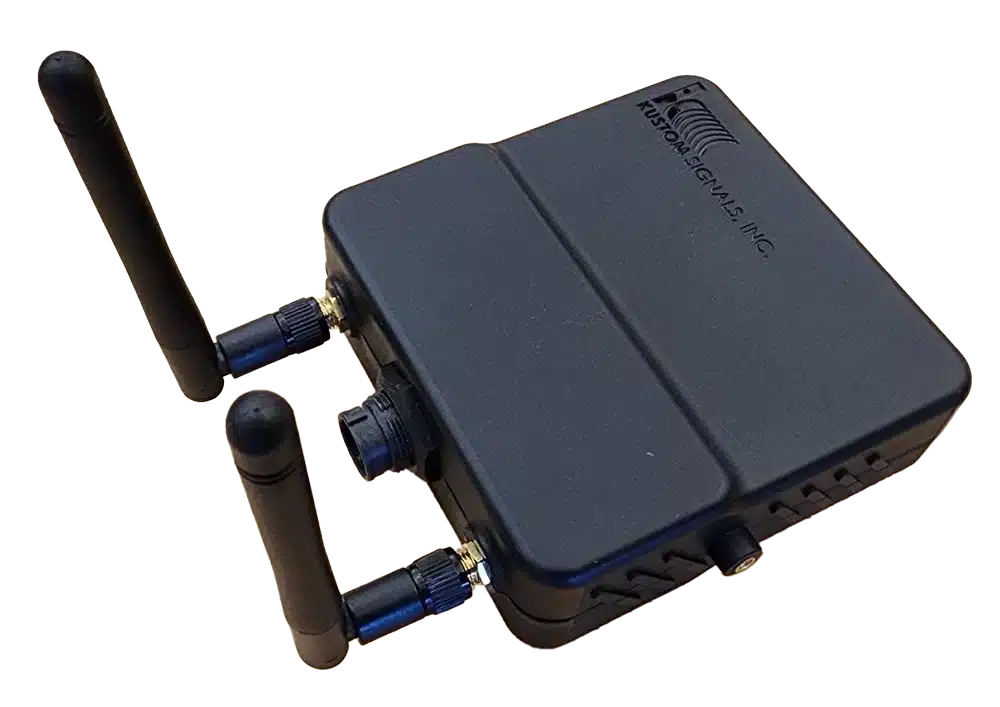
The Results
EyePortal was successful on many levels. The initial prototype hardware worked without changes and only minor updates to the case tooling were required, saving substantial time and money. The product is a hit in the field and related technology was subsequently patented.
This patent builds upon the integration of our hardware and software systems to work together in unison, a core feature of the EyePortal product launch. Launching the ability to activate either the Vantage Body Worn Camera or the Eyewitness HD In-Car Video System from the other device allows the officer to focus on the situation, and less on operation.
Kustom Signals
Press Release