Hardware Design
Systematic Consulting Group delivers quality hardware development services.
The Solution to Your
Hardware Design Service Challenges
We pair you with a hardware design engineer and project team who are well equipped with the professional expertise and hands-on skills to handle your entire hardware design project based on your specific requirements. Your dedicated engineer and team will work diligently with you from the conceptualization stage through testing to production.
Our hardware engineering services include programmable logic, PCB layout, and board design that integrates microprocessors, DSPs, FPGAs, and complicated RF, analog, and power systems, from the architecture phase through production support. At Systematic Consulting Group, hardware design specifications are our top priority. We guarantee that your next hardware design project will surpass your expectations.
Stages of Product Development Lifecycle
There are various stages in our hardware design process that ensure sophisticated and efficient product quality.
Stages of Product Development Lifecycle
There are various stages in our hardware design process that ensure sophisticated and efficient product quality.
Key Elements Our Hardware Engineers
Keep In Mind During the Hardware Design Process
Key Elements Our Hardware Engineers Keep In Mind During the Hardware Design Process
Operational Environment
We build the system to tolerate the anticipated environmental requirements and conditions. Systems that operate indoors will possess different requirements and specifications than a system that operates outdoors in all weather conditions.
Operational Temperature
We take into consideration the operational temperature of the device at any given time and situation. Aside from temperature, we also put factors such as range, pressure, humidity, required ruggedness, and exposure to radiation in the design and validation phases.
Power Dissipation
and Thermal Analysis
Thermal dissipation is always a critical issue we watch out for while building our hardware devices, with proper analysis duly carried out during the design and simulation phases.
Provision for Feature Upgrade
While building embedded systems, we always keep in mind the possibilities of later feature upgrades. If we know a feature or upgrade may be coming soon, we create the channel through which it can be upgraded in the future.
Industries We Serve
Our hardware design services have applications in many industries.
Healthcare
Systematic Consulting Group provides hardware design services to support the healthcare industry. Through these partnerships, we have helped companies through the lengthy regulatory processes of bringing an FDA-approved product to market, including proof of concept, prototyping, risk management, product verification, clinical research, and production phases. Let us help bring novel features to your existing devices or build an entirely fresh component at a very affordable cost.
Sports and Gaming
We develop hardware devices and gadgets to power the gaming industry. Our work has helped athletes and hobby players alike improve their technique. Devices like our launch monitor product help players augment their skills for the field or course.
Food Retail
Both small and large companies in the food retail industry utilize our hardware design services at various levels of their business operations. We are strategically positioned to help all industries grow including this customer-facing industry.
Manufacturing
Systematic Consulting Group designs hardware for industrial line automation in cases where off-the-shelf PLCs or IO boards don’t suffice.
Law Enforcement Industry
Technology plays an increasingly significant role in the detection and prevention of crimes. From in-vehicle computers to speed up the data collection process to automatic license plate scanning technology to drones that allow officers to safely monitor an area, our hardware development services help the players in this industry keep their communities safe.
Our Proficiency
Tools:
Our Partnerships
We partner with big brands to engineer innovative products that enhance the lives of our teeming customers across the globe. Here are just a few:
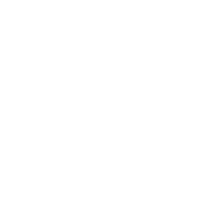
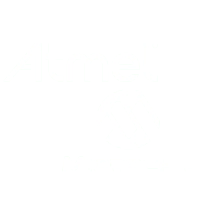
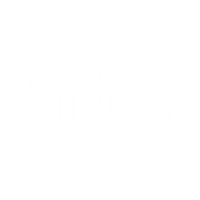
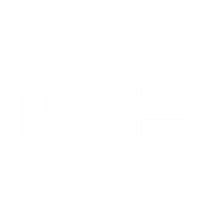
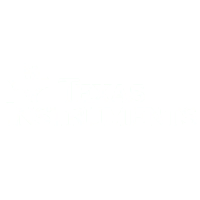
Why Work with Systematic Consulting Group?
Many top brands prefer us for the following reasons and more: